Unlocking Success in Metal Fabrication with Advanced Plastic Injection Mold Tooling
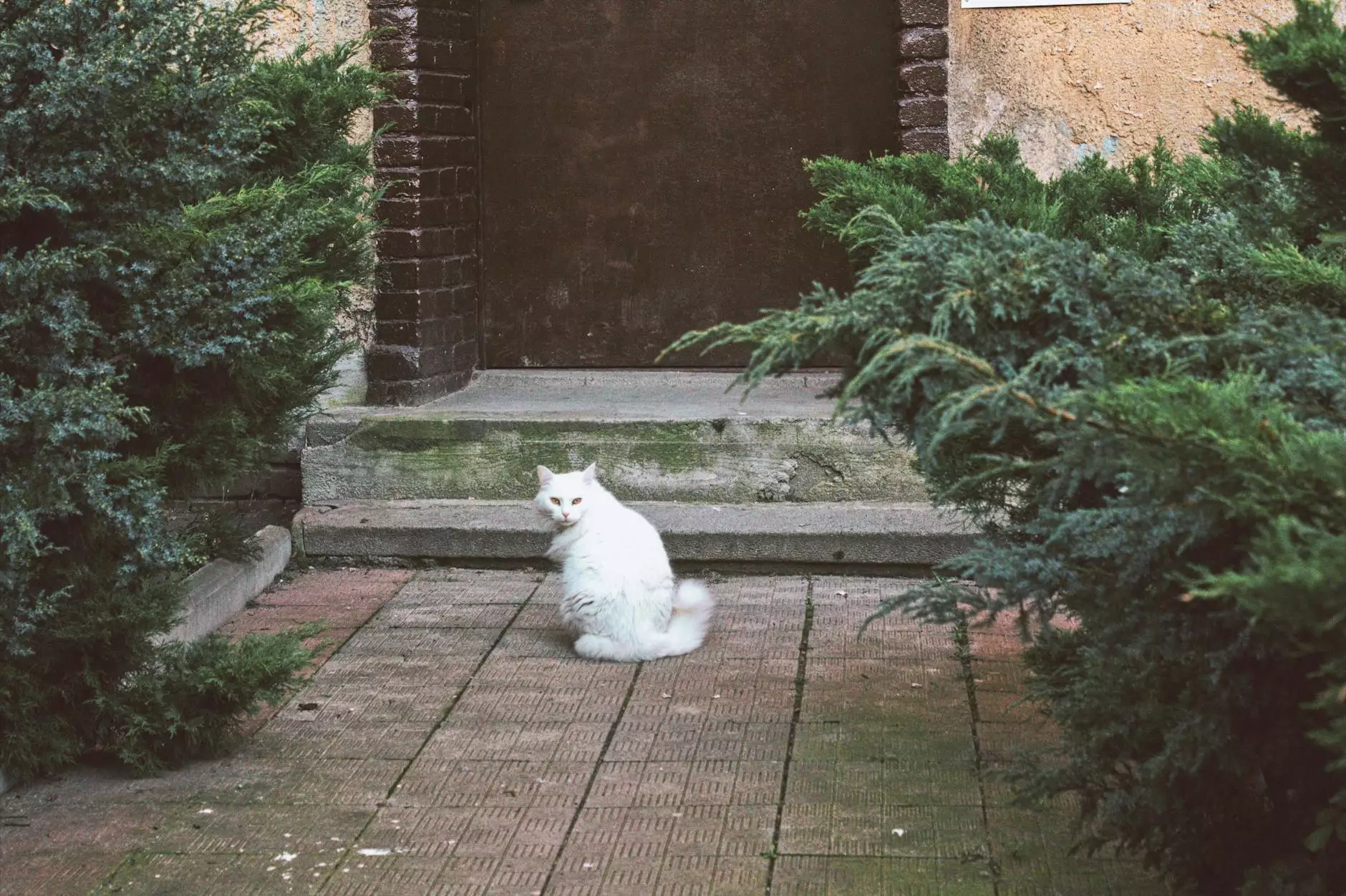
In the highly competitive world of metal fabrication, precision, efficiency, and innovation are the cornerstones of success. Central to achieving these objectives is the mastery of plastic injection mold tooling—a pivotal process that influences the quality, production speed, and cost-effectiveness of manufacturing operations. As industry leaders like DeepMould revolutionize the field, understanding the intricacies and latest advancements in plastic injection mold tooling becomes essential for manufacturers aiming to stay ahead. This comprehensive guide delves deep into the significance, design principles, technological innovations, and best practices that underpin successful mold tooling in metal fabrication, empowering you to make informed decisions for your manufacturing needs.
Understanding Plastic Injection Mold Tooling in Metal Fabrication
At its core, plastic injection mold tooling involves creating precise and durable molds used to manufacture plastic components through the injection molding process. While traditionally associated with plastic production, its principles, design techniques, and technological advancements profoundly impact metal fabrication industries, especially in scenarios where composite materials or hybrid manufacturing processes are involved.
Specifically, in the realm of metal fabricators, plastic injection mold tooling is employed to produce complex, high-precision plastic parts that complement metal components, enabling integrated manufacturing solutions. The synergy between plastic and metal components enhances product performance, reduces weight, and streamlines assembly processes, illustrating the strategic importance of advanced mold tooling in modern manufacturing.
Why Plastic Injection Mold Tooling Is Critical for Modern Metal Fabrication
- Enhanced Precision and Detail: High-quality mold tooling ensures the production of intricate plastic parts with tight tolerances, crucial for components requiring exact specifications in metal assemblies.
- Cost Efficiency: Investing in durable, well-designed molds reduces material waste, minimizes defects, and accelerates production cycles, leading to significant cost savings over time.
- Rapid Prototyping and Product Development: Advanced tooling allows for swift iteration, enabling manufacturers to test and refine designs before committing to full-scale production.
- Versatility and Customization: Modern molds accommodate complex geometries and multi-material components, broadening design possibilities and functional integration.
- Quality Consistency: Reliable mold tooling guarantees consistent output, vital for maintaining high standards in metal-part assembly and overall product quality.
Key Elements of Successful Plastic Injection Mold Tooling
Achieving excellence in plastic injection mold tooling requires meticulous attention to several critical components:
1. Design Accuracy and Precision
An effective mold begins with detailed design processes that incorporate advanced CAD (Computer-Aided Design) and CAE (Computer-Aided Engineering) tools. These facilitate simulation and analysis, predicting how plastics will fill the mold and identifying potential issues before production, thereby ensuring the mold’s accuracy and functionality.
2. Material Selection for Mold Construction
The choice of mold materials—such as high-grade steel, tungsten, or aluminum—impacts durability, wear resistance, and thermal conductivity. Selecting appropriate materials tailored to production volume and part complexity is vital for longevity and performance.
3. Mold Fabrication Technologies
Advanced manufacturing techniques such as CNC machining, electro-discharge machining (EDM), and additive manufacturing are employed to craft precise mold components. These technologies enable complex geometries, reduce lead times, and enhance overall mold quality.
4. Thermal Management
Effective cooling channels and thermal regulation elements are integrated into molds to control temperature variations, improve cycle times, and maintain dimensional stability during injection and ejection processes.
5. Surface Finishing and Coatings
Surfacing treatments, including polishing, texturing, and applying release or anti-adhesion coatings, optimize plastic flow, reduce defects, and facilitate easy mold release, thereby improving part quality and mold lifespan.
Innovative Trends in Plastic Injection Mold Tooling
The industry continually evolves through technological innovation, enabling more efficient, sustainable, and complex mold designs:
Smart Mold Technology
Embedding sensors within molds provides real-time monitoring of temperature, pressure, and wear, allowing predictive maintenance and minimizing downtime.
Composite and Multi-Material Molds
The development of molds capable of handling multiple materials or creating multi-shot parts enhances design versatility and reduces assembly steps.
Additive Manufacturing for Mold Production
3D printing enables rapid prototyping and the fabrication of complex mold components that are difficult or impossible to produce using traditional methods, significantly reducing time-to-market.
Sustainable and Eco-Friendly Approaches
Materials and processes that lower energy consumption, utilize recyclable mold materials, and minimize waste are gaining prominence, aligning manufacturing with environmental responsibility.
Best Practices for Optimizing Plastic Injection Mold Tooling
To harness the full potential of plastic injection mold tooling, manufacturers should adhere to industry best practices:
- Close Collaboration: Engage with experienced mold designers, material scientists, and manufacturing specialists from the initial concept to ensure design for manufacturability.
- Thorough Testing and Validation: Conduct rigorous mold flow analysis, prototype testing, and iterative revisions to refine tooling and prevent costly errors.
- Implementing Quality Control: Use precise measurement tools and inspection processes to verify mold dimensions, surface finishes, and functional features before full production.
- Preventive Maintenance: Schedule regular inspections and maintenance routines to extend mold life and maintain consistent part quality.
- Leveraging Technology: Incorporate automation, real-time data monitoring, and advanced engineering software to streamline operations and enhance precision.
Choosing the Right Plastic Injection Mold Tooling Partner
Partnering with a reputable provider like DeepMould ensures access to cutting-edge technology, comprehensive service, and expert guidance. Key considerations when selecting a mold manufacturer include:
- Experience and Industry Track Record: Proven expertise in plastic injection mold tooling for diverse industries.
- Technological Capabilities: Availability of advanced machining, design software, and innovative production methods.
- Quality Standards: Certifications such as ISO 9001, ensuring consistent quality and adherence to international standards.
- Customer-Centric Approach: Transparent communication, flexible solutions, and post-sales support.
- Cost and Lead Time: Competitive pricing coupled with efficient production schedules.
Conclusion: Elevating Metal Fabrication with Superior Plastic Injection Mold Tooling
In the dynamic landscape of metal fabrication, the role of plastic injection mold tooling goes far beyond merely creating plastic parts. It is a strategic asset that influences product quality, manufacturing efficiency, and innovation capacity. By investing in advanced design, leveraging cutting-edge technologies, and partnering with industry leaders like DeepMould, businesses can unlock new levels of productivity and product excellence.
As the industry continues to evolve with smarter, more sustainable, and more intricate mold systems, embracing these advancements ensures you remain at the forefront of manufacturing innovation. Whether developing new components, optimizing existing processes, or pioneering hybrid manufacturing solutions, mastery of plastic injection mold tooling is essential for success in modern metal fabrication and beyond.
Takeaway Points for Excellence in Plastic Injection Mold Tooling
- Precision design and materials are fundamental to durable, high-quality molds.
- Technological innovations like smart sensors and additive manufacturing revolutionize mold creation and maintenance.
- Collaborating with expert partners ensures optimal results and minimized risks.
- Adopting sustainable practices aligns manufacturing excellence with environmental responsibility.
Embrace the future of plastic injection mold tooling today, and position your manufacturing enterprise for sustained growth, innovation, and excellence in the competitive landscape of metal fabrication.