Die Casting Production: A Comprehensive Guide to Metal Fabrication
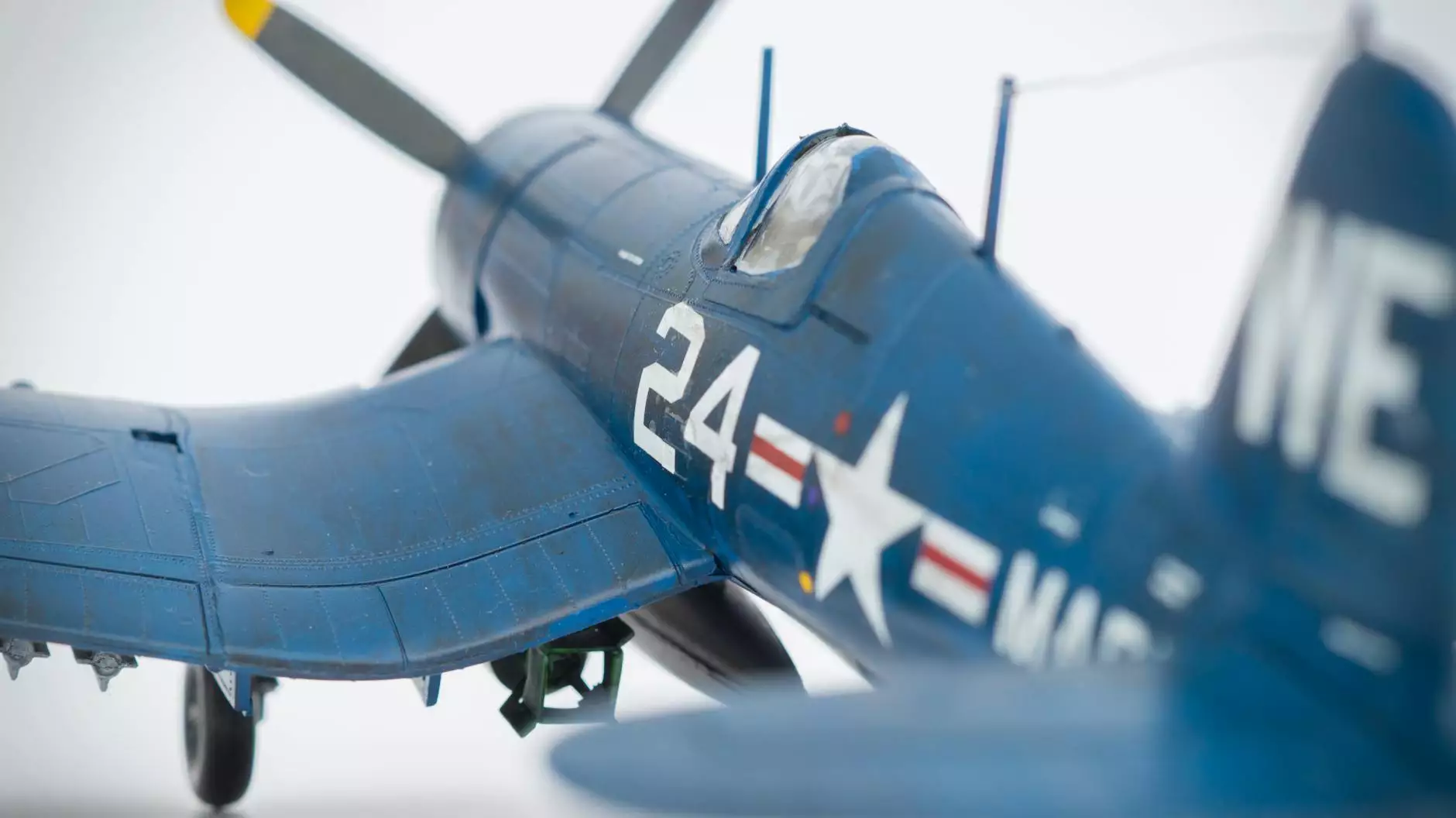
In the world of manufacturing, few processes are as efficient, versatile, and reliable as die casting production. This method has changed the landscape of metal fabrication, allowing businesses to create complex shapes with remarkable precision. In this article, we will delve into the intricacies of die casting, explore its advantages, and explain its various applications within different industries.
What is Die Casting?
Die casting is a metal casting process characterized by the forcing molten metal under high pressure into a mold cavity. The mold, commonly referred to as a die, produces detailed and intricate components that are often used in various products. This process has been used for over a century and is known for its ability to produce large quantities of parts with outstanding dimensional accuracy and smooth surfaces.
How Does Die Casting Work?
The die casting process involves several key steps:
- Melt Preparation: The metal, usually aluminum, zinc, or magnesium, is heated in a furnace until it reaches a liquid state.
- Injection: The molten metal is injected under high pressure into the die. This pressure ensures that the cavity is completely filled.
- Cooling: The molten metal remains in the die until it cools and solidifies, typically within a few seconds.
- Ejection: Once solidified, a mechanism ejects the casting from the die, allowing for a new cycle to begin.
Types of Die Casting
There are two primary types of die casting: hot chamber and cold chamber die casting. Understanding the differences between these methods is crucial for selecting the most appropriate technique for a given project.
Hot Chamber Die Casting
Hot chamber die casting is typically used for metals with low melting points, such as zinc. The injection mechanism is located within the furnace, allowing molten metal to flow directly into the chamber:
- Advantages: Faster cycle times and reduced equipment costs.
- Disadvantages: Limited to low-melting point metals and lower casting weights.
Cold Chamber Die Casting
Cold chamber die casting is more suited for metals with higher melting points, including aluminum and magnesium. The molten metal is poured into the injection chamber before being injected into the die. Key features include:
- Advantages: Capability to cast high-melting point metals and versatility in product design.
- Disadvantages: Slower cycle times and potentially higher costs due to complex machinery.
Advantages of Die Casting Production
Die casting production offers numerous benefits, making it a preferred method for many manufacturers:
1. High Production Rates
One of the most significant advantages is the ability to produce large volumes of parts quickly. Die casting can yield thousands of identical components per hour, making it ideal for mass production.
2. Precision and Accuracy
Die casting produces components with exceptional dimensional accuracy, often within ±0.005 inches. This precision reduces the need for secondary machining, saving time and money.
3. Excellent Surface Finish
The nature of die casting creates smooth surfaces, which often require minimal finishing processes. This characteristic is particularly important in aesthetic applications where visual appearance is crucial.
4. Material Efficiency
Die casting minimizes waste material, as the process produces near-net-shape components. This efficiency is not only cost-effective, but it also supports environmentally sustainable practices.
5. Design Flexibility
The versatility of die casting allows for the production of complex shapes and designs. Manufacturers can create intricate features without sacrificing strength or integrity.
Applications of Die Casting Production
The versatility of die casting production means it's used across various industries:
1. Automotive Industry
The automotive industry relies heavily on die casting for producing lightweight yet strong components, such as:
- Engine blocks
- Transmission housings
- Suspension components
2. Aerospace Industry
Die casting is also essential in the aerospace sector, contributing to:
- Structural components
- Engine parts
- Fuel systems
3. Electronics Industry
Electrical housings and components crafted through die casting are known for their durability and precision, making them vital in consumer electronics.
4. Consumer Goods
From kitchen appliances to decorative items, many consumer goods utilize die casting for efficiency and aesthetics.
Quality Control in Die Casting Production
To ensure that die cast components meet strict standards, meticulous quality control measures are applied at every stage of production:
1. Material Testing
Testing the composition of the raw materials ensures they conform to specified standards, preventing deficiencies in the final products.
2. Process Monitoring
Monitoring temperature, pressure, and timing during the die casting process guarantees adherence to production parameters, enhancing consistency.
3. Final Inspection
Final inspection of the die cast products is essential. Techniques such as dimensional checks, surface analysis, and non-destructive testing (NDT) are employed.
The Future of Die Casting Production
As technology continues to evolve, so does the field of die casting production. Innovations such as:
- 3D Printing: This technology is being integrated into die casting to create more complex and detailed tooling.
- Automation: Increased automation is streamlining production processes and reducing the likelihood of human error.
- Alloy Development: New metal alloys are being developed to enhance performance characteristics and sustainability.
Conclusion
In summary, die casting production stands as a cornerstone of modern metal fabrication. Its ability to produce high-quality, precise components efficiently makes it a preferred manufacturing method for a wide array of industries. As the technology continues to evolve, die casting will undoubtedly play an even more significant role in shaping the future of manufacturing. For businesses looking to leverage the advantages of die casting, partnering with reliable and experienced providers like deepmould.net is essential. Their expertise in metal fabrication and die casting production can help you achieve your manufacturing goals effectively and efficiently.